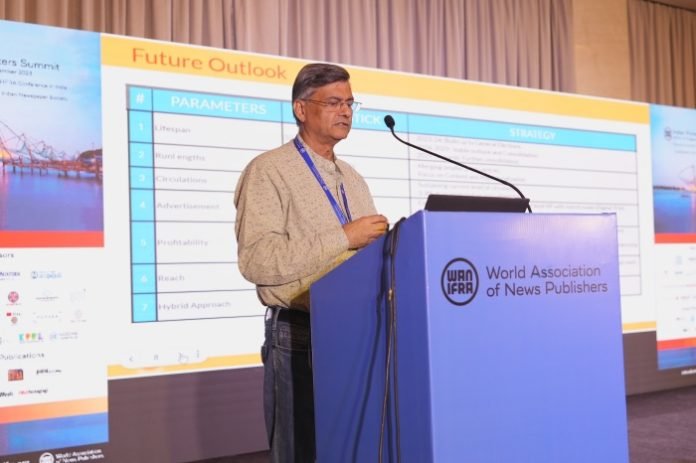
An important point of discussion at the Wan-Ifra Kochi printers’ meet in September was a strategic shift toward better plate technology in order to optimize cost and efficiency. An interesting presentation on the subject by RD Bhatnagar, former Chief Technology Officer, DB Corp, led to an intense discussion on the subject wherein the participants called for collaboration between publishers.
Bhatnagar’s presentation began with global warming and how all printing materials such as newsprint, inks, plates, and printing processes are highly sensitive to ambient temperatures. Giving a general idea of the global print market trends, he explained how the newspaper and commercial printing markets are shrinking everywhere, and how printers are making a shift to packaging and from offset to digital.
In India, however, publishing is still strong, where newspapers and some commercial markets are performing well. In such a scenario, there is a need to enhance collaboration, secure our supply chain requirements, and reduce dependence on global players, he explained.
Giving an overview of the global plate market, Bhatnagar said the key players are Agfa, Fuji, Kodak, Lucky, TechNova, IBF, and a few others. However, the consolidation of the industry has reduced more than 30 plate manufacturers, to about 10 focused players.
The availability of litho-grade aluminum, used in offset plates, is a challenge as litho suppliers are shifting to EV auto-grade aluminum. Plate technologies are also moving towards chemistry-free and process-less, he explained. “The global players are exploring alternatives to China and India is a preferred destination for the China plus one strategy,” Bhatnagar said. He said India has an advantage as it is a new manufacturing hub, has a growing economy, a stable government, and the ease of doing business is improving. In addition, the presence of a young workforce is a strong point, and there is increased global acceptance due to stronger relationships as well as more transparent policies. The shift away from China, on the other hand, is because of global sentiments after the pandemic, focus on alternative manufacturing sites and supply chains, and geopolitics.
Giving a general idea of offset plate users, Bhatnagar categorized them into packaging, newspapers, commercial printing, and other publications. In packaging, plates have a high growth potential for the next 5-10 years because of the present low per capita consumption, and export potential. India, he said, can play the role of a manufacturing hub in this segment.
Newspapers in India are still holding strong because of the advertising-driven model. There is growth potential in tier 2 and 3 markets and the language press because of improved literacy rates. This will ensure the growth of offset plates in this segment for another 5 years. According to him, commercial printing is where the real challenge lies. At present, there is a hybridization of commercial, packaging, and digital. The key drivers are diversification to packaging and value innovation through digital. Nevertheless, he said this segment, still has some steam left in tier 2/3 markets.
Explaining the evolution of plate technologies, he said from wipe-on plates in the 1970s to PS offset plates, CTF, CtP thermal, CtP violet, and now process-less thermal and zero pre-heat violet, we have come a long way. PS Offset Plates, introduced around 1980, reduced manual processing steps as the plates could be imaged directly from films. This eliminated the need for camera work. The 1990s were the times of CTF when there was a direct digital output of films from the computer – eventually leading to full broadsheet pages, including halftones.
Then came CtP-thermal in 2000, which replaced CTF, as there was direct imaging of printing plates. Introduced around 2010, CtP-violet became the first choice of newspapers because of its robustness, speed, quality, and eco-friendliness. Now we have something called process-free thermal as well as zero pre-heat violet plates – while the former is gaining traction amongst newspapers also, the latter’s development is in the advanced stages. About 83% of the present newspaper market is on CtP violet technology, he suggested. In thermal zero process plates, the move is direct from imaging in the output device or platesetter – to print. “To sum it up, as processes get eliminated, we save time, effort, and money,” Bhatnagar said.
The percentage share of plate cost in the overall operation expenditure, though small, still has immense value and hence there is a need to optimize it. Newsprint has a 65% share in the overall opex, manpower and miscellaneous 21%, plates 6%, ink 6% while chemicals and blankets have a 2% share. However, if newsprint is left out, then plate cost in the overall opex is 17% (15% – net of scrap), manpower and miscellaneous go to 60%, ink to 17%, and the chemicals and blankets share goes to 6%.
Since 90% of the global newspaper printing is offset, he said, the industry is heavily in the system where transformation won’t be easy even if newer and better technologies arrive – as scrapping the old machines purchased at a humongous cost is out of the question. And so the answer lies in optimization. “It is very important to have the right plate technology that can offer robust compatibility with the ecosystem,” Bhatnagar said. He spoke of research in new technologies that are still unproven in efficacy and cost.
“Select a technology robust enough to handle challenges related to older machines, various types of newsprint, inks, chemicals, and more. While experimentation is encouraged, it should not come at the expense of standardization.” He cautioned that multiple technologies would mean multiple inventories, pre-press setups, and inconsistency in print. Other tips from Bhatnagar included continuing to use the existing tech as long as it remains functional to extend the lifespan of machines. Avoid new investments. Look at options such as 0.20 mm plates for smaller editions.
The presentation led to a round of debate and discussions with Snehashish Roy of BCCL explaining how plate cost is a cause for concern for small newspapers with low circulations as they need to change plates for all editions no matter how small the print runs would be. He advocated the need to collaborate to find a way out. While Technova’s Amit Khurana stressed the need for reducing the costs within the current infrastructure, the Kodak representatives at Kochi, highlighted their process-free plate technologies that have gained traction amongst Indian newspapers. Loyalists of violet plates pointed to the price factor.
Bhatnagar concluded with a word of advice for print news media. “Newspapers will have to develop innovative strategies for staying relevant for the next generations who will consume media in a very different way than we did.”