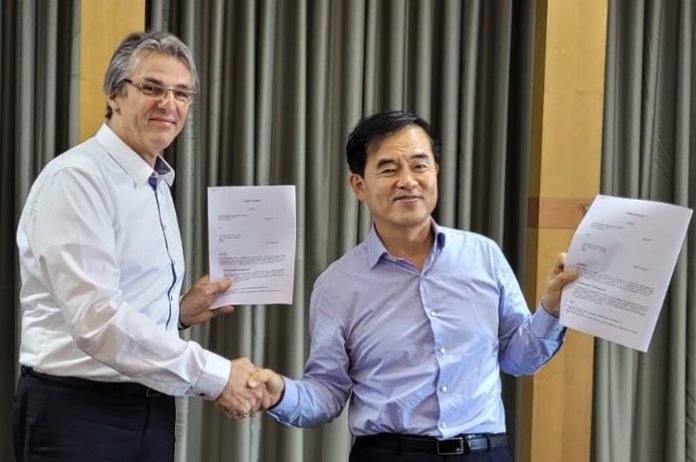
Manroland Goss Web Systems vice president Sales International Heiko Ritscher answers some questions about the news media industry, its current outlook, and modernization plans put to him by Naresh Khanna of Indian Printer and Publisher. He also says that customers buying new presses have a future vision that still relies on the need and strengths of a printed product in combination with other media channels.
Indian Printer and Publisher – How can we generally describe the worldwide activity of the news media industry, especially with regard to print and particularly the renewal and modernization of presses and the purchases of new presses?
Heiko Ritscher – On one side, the worldwide newspaper industry continues to be in a process of strong consolidation – reducing circulations and pagination. This leads to a generally more restrictive investment policy.
On the other hand, there have been only a limited number of investments in new equipment during the last decade and the installed base of many newspaper printers is relatively old, with electronic obsolescence issues and higher operational costs including higher manning needs.
Against this background, we see two investment tendencies of newspapers:
- Investment projects into electronic and automation upgrades to ensure the availability of spare parts for the next decade and also to reduce operational costs;
- and, investment into new presses with high automation, the latest technology, and low operational cost.
Certainly, newspapers investing in new equipment still have long-term planning and/or think about this alternative because of a specific need such as consolidation from several to only one printing center or considerable reductions in the operational cost.
IPP – Can any trends be seen or meaningfully talked about – such as the refurbishment of old presses, new efficiencies from retrofitted automation, and better control software?
Heiko Ritscher – One of the main reasons for upgrading an older press is the electronic obsolescence, unavailability of spare parts, and/or unpredictable long delivery times for them combined with a drastically increased cost because of reduced production volumes up to single manufacturing. In a few words, the reason for upgrading would be to ensure that the press still can do its work.
Of course, there also are some possibilities of implanting new and additional functionalities helping to reduce the operational cost and or improve the efficiencies. And manroland Goss can and is offering many of them. With a new press, those possibilities are of course much higher.
IPP – Speaking of new presses you have a new customer in Asia in South Korea. What are the automation and efficiency features of the brand new 4 x 1 press purchased by the Hankyung Group which publishes The Korea Economic Daily? And how do these features help the viability and improve the carbon footprint of new presses and new newspaper plants?
Heiko Ritscher – Each of the press lines [purchased by the Hankyung Group] can produce up to 95,000 copies an hour with a pagination of up to 48 pages broadsheet in a flexible book structure. This high performance in combination with all the automation features is the key to efficient and productive newsprint production.
The Colorman e:lines purchased by the Korean customer have the full range of the latest automation features such as the whole bundle of inline controls for register, density, fan-out, automated plate loading, automated roller, and blanket washers, just to mention some of them. They are helping to reduce the staffing on the presses, changeover times, wastage, and therefore consumables such as paper and ink.
The presses will be equipped with an automated reel supply system and the complete reel area can be operated by only 2-3 operators. The presses will be delivered with the latest version of our PECOM controls with extensive possibilities of pre-adjustments of the presses for each new job and sophisticated online support possibilities.
And, on top of it, most of the above-mentioned automation components such as the inline controls, automatic blanket washers, the PECOM controls, and others are coming out of the manroland Goss product portfolio with an optimized interaction which gives an additional boost to the press productivity and efficiencies.
IPP – What are the dynamic cost considerations of some of the recent buyers of new double-width press around the world? – In other words, how are they looking at the viability of these projects and their returns on investments?
Heiko Ritscher – The reasons for the decisions to invest in new equipment are diverse. What is the focus point always in the decision process – that’s a considerable reduction in the operational cost as the main driver for an acceptable return on investment.
Often the projects are linked to a change of the current, often highly up-valued location into a new location in an industrial area. Some projects have a focus on consolidating two or more production sites into one or a new press substituting two or three existing press lines with all the cost savings related to this.
Another important element in the decision process is the possibility of a considerable reduction of people operating the presses by implementing the highest possible level of automation. The number of necessary operators is one of the most important cost drivers in the regions where we sold new equipment.
As paper costs also increased dramatically, some projects are linked to a format change while maintaining the printed area. This means a reduction of the non-printed area. Those are only some of the important decision drivers. And last but not least, our customers buying new presses have a future vision that still relies on the need and strengths of a printed product in combination with other media channels.