The German printing company C H Beck reacts to the smaller book runs by investing in a highly automated web offset press tailored for quick plate changes. The smooth plate supply is ensured by an equally individual logistic solution from Beil.
Founded in 1763, the printing house C H Beck with around 300 employees produces brochures, hardcovers, loose-leaf works, magazines, technical documentation, and electronic publications for the publishing house of the same name and many other companies. C H Beck is a leader in Europe when it comes to high-quality and page-heavy books on thin paper.
In January 2020, the world’s most modern web offset press for printing products on thin and book-printing paper went into operation in Nördlingen. According to the company, this is remarkable as in Germany, the last installed new web offset press for books is about 15 years ago. C H Beck broke this long-lasting trend by investing around seven million euros in a manroland Goss Lithoman auto print, including plate feeder and product disposal, thus ushering in a new era in offset printing for books. It replaced a book printing line that had been in operation for nearly four decades.
The company claims that with the new technology, including printing plate feeders, folding systems, and product disposal, print shops can print papers between 22 and 100 g/sqm with even higher quality and productivity. Such an extensive range of substrates was not possible with the offset printing presses currently in use on the market, as well as the digital printing presses currently in use. Runs as small as 800 copies are no problem with the state-of-the-art control electronics.
Declining runs lead to high plate demand
Declining circulations characterize the situation in book production, but an increasing number of titles. Books become more individual, and book programs are updated at ever shorter intervals. With the latest investment, C H Beck has addressed the plate change and setup process. Now plate changes are possible even during operation, the company claims. Simultaneously, the printing speed of 35,000 prints in an hour can be fully utilized at higher runs. The machine is also intended to prove that the offset process can be used to produce books in small editions successfully. About two years passed from the conception of the new production line to its completion and installation.
Beil-Registersysteme was chosen to design and implement the logistics concept for the project. The contact between Beck and Beil has existed for many decades – via the manual devices used in Nördlingen. The latest project has now been implemented together with manroland Goss and Hans Lüscher.
Plate trolleys with removable gondolas
The logistics solution consists of several plate trolleys with a removable gondola for eight bent 1,470 x 1,292 mm plates. A lifter system installed next to the reel splicer, which lifts the removable gondolas (the car remains on the ground) to gallery height, and a rail system on the gallery of the printing press for moving and buffering several gondolas. According to the company, this simplifies plate transport and allows the reliable delivery of printing plates directly to the lower and upper printing units.
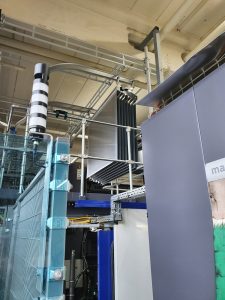
“This system of printing plate logistics is indispensable for the full utilization of the rotation; a manual transport of the printing plates to the printing units would make the whole concept impossible. In addition, networking in Beck’s production is ‘very important'”, as Uwe Bauhammer, head of Printing, confirms. As many machines as possible should be included. Keywords such as automated order data exchange and interface automation are part of the production strategy. The ‘marriage’ of the gondola and the printing plate sets for the new book line takes place, for example, via barcode readers. The print jobs and the associated plates on the gondolas are displayed on monitors.
According to the press release, the printing plate logistics in this production area of the printing company C H Beck can be expanded in the future by integrating the complete plate production department into a closed and fully automatic system. However, even the current expansion stage leads to an improved efficiency healthy for the existing staff. Less manual intervention, for example, reduces the risk of damage to plates, and the barcode organization ensures the correct processing of the production plan. The results are said to be reduced waste and greater overall efficiency for the new production process.
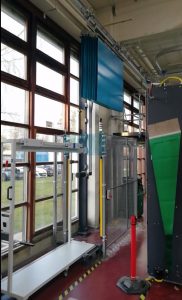
Flying plate change
The improved plate transport ultimately ensures the replenishment for the numerous plate changes, which sometimes follow each other within a few minutes. Despite small print runs, Beck plans to print around 1.2 million pages per hour or up to eight billion pages per year with the new production line. The system can operate format heights of up to 200 mm – ideal for paperback areas. Due to the two printing units, either 1/1-coloured can be printed with a flying plate change or a 2/2 color.
On 13 January 2020, the new web offset press with the first official order, titled ‘Simenon – Die Marie vom Hafen’, was put into operation. In the first few months, the performance continued to rise. “In retrospect,” says printing manager Uwe Bauhammer, “was the decision for the plate logistics solution from Beil just right. Six months after implementing the new production system from Beil, the concept is working exactly as expected, allowing C H Beck to compete in today’s short-run book market place effectively.”