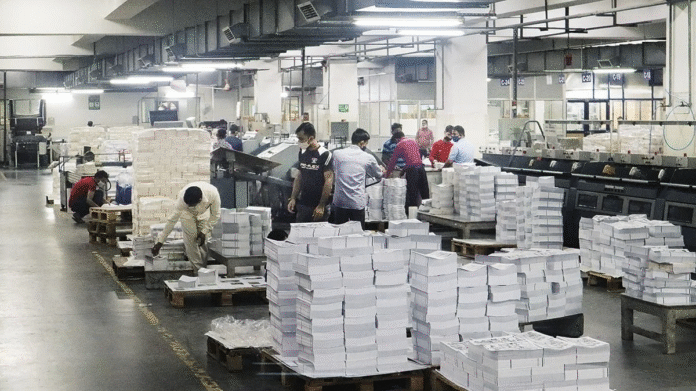
- Get certified for environmental responsibility: ISO 14001, a globally recognized certification, proves your company manages its environmental impact properly.
Hire ISO 14001 consultant. List processes impacting the environment such as water, energy, waste and set goals to reduce impacts. Monitor and pass an audit by a certifying agency (TÜV, BSI, or SGS). Measure if you have a valid ISO 14001 certificate.
- Use FSC- or PEFC-certified paper: Certification ensures the paper is sourced from responsibly managed forests.
Ask your paper supplier for certified paper. Request the custody certificate chain, keep it in records. Mention the certification on job sheets or invoices. Measure certified percentage of your paper usage. (Target: 100%)
- Become a carbon-neutral printer: Offset carbon emission through clean energy or carbon credit purchases.
List energy uses: electricity, fuel, logistics, etc. Use a calculator (GHG protocol tools or hire a consultant) to measure annual carbon footprint. Buy certified carbon offsets or install solar panels to reduce impact. Get certified by a carbon-neutral registry. Measure total emissions (kg CO₂e/year); % offset (target: 100%)
- Use water-based inks: Safer for all with fewer harmful fumes (VOCs).
Ask ink supplier for low-VOC, vegetable- or water-based inks. Train team on usage and drying times. Get technical sheets for each ink type. Measure % of jobs printed using water/vegetable-based inks.
- Stock recycled paper options: Reduces waste, saves trees.
Stock paper with 30%-100% post-consumer waste. Request documentation on recycled content. Offer it as a ‘green upgrade’ to clients. Measure % of total orders printed on recycled paper.
- Reduce harmful chemical fumes (VOC control): These are toxic fumes from solvents and inks, harmful for health and air quality.
Go for low-VOC versions. Install ventilation hoods and scrubbers in press areas.
Monitor air quality quarterly using a VOC meter. Measure VOC emissions in ppm (parts per million). Keep below legal limits.
- Upgrade to energy-efficient presses: These use less power, produce less waste, save costs.
Replace old offset presses with better machines. Once printing done, it should get converted into the final product in 24 hours. Measure electricity used per ton of printed material (kWh/ton).
- Use renewable energy: Solar or wind energy reduces carbon footprint.
Install rooftop solar panels or ask electricity provider for a ‘green energy’ package or
purchase renewable energy certificates. Measure electricity sourced from renewables (target: 100%)
- Use digital printing: Efficient for small orders and reduce waste.
Invest in a digital press like HP Indigo or Konica Minolta. Train staff. Offer on-demand printing for reprints or custom versions. Measure % of short runs moved from offset to digital.
- Set up a recycling program: Recycle paper, plates, cartridges, and plastics.
Place clearly marked bins for each waste type. Sign pickup contracts with local recyclers and keep a log. Measure monthly recycling rate by weight (Target: 90%+).
- Reduce paper waste with better layouts: Smart layouts = less unused paper = cost + waste savings.
Use layout software (e.g., Kodak Preps) to optimize ganging and imposition. Recommend trim sizes to reduce offcuts. Design sample dummies with clients to minimize blank pages. Measure paper utilization rate (% used vs. waste).
- Embrace circular practices: Keep materials in use longer.
Use paper scraps for packaging or filler. Convert returned or outdated books into cartons or pads. Reuse aluminum plates and packing. Measure % of waste reused internally or returned to suppliers.
- Save water with modern equipment: Old processes waste water.
Shift to ‘chemical-free’ plate systems that use less water. Install flow restrictors on taps and hoses.
Reuse treated wastewater for landscaping or cleaning. Measure eater usage per ton of print output.
- Replace hazardous chemicals (REACH compliance): Avoid banned chemicals.
Ask for material safety data sheets from suppliers. Check for banned chemicals, switch to certified alternatives. Measure % of materials reviewed and REACH compliant.
- Design books for easy recycling: Recycled books offer a competitive advantage.
Use recyclable materials: No PVC coating, plastic covers, or foil blocking unless absolutely needed. Opt for PUR or water-based adhesives over EVA. Standardize sizes and bindings to make disassembly easier in recycling plants. Avoid combining cloth, metal, plastic on covers. Measure % of books printed using fully recyclable components and % reduction in plastic-based finishes.
- Only green suppliers: Your environmental promise is as strong as your vendors.
Work with those who offer FSC-certified, REACH-compliant, and recycled inputs. Request yearly environmental statements. Measure % of suppliers reviewed annually for compliance.
- Audit vendors for sustainability: Regular checks makes your supply chain clean.
Conduct assessments and visit high-risk vendors for on-site audit. Use standard checklists. Measure % of vendors passing sustainability checks.
- Cut transport pollution: Shipping materials long distances = more emissions.
Order in bulk and prefer local suppliers if possible. Use consolidated shipping for deliveries. Measure emissions per shipment (kg CO₂e per km).
- Track, share sustainability metrics: Data builds trust, drives improvement.
Set monthly KPIs for energy, waste, paper, water, emissions. Publish a one-page sustainability report every year. Share your monthly wins on LinkedIn. Measure monthly trends in key areas.
- Offer carbon footprint reports per print job: Clients want to know each print run’s footprint.
Use ISO 16759 to calculate emissions per job. Include paper, ink, transport, and electricity. Measure CO₂e per unit/book for major projects.
- Get independent sustainability rating: Third-party stamp proves commitment.
Apply for EcoVadis, CDP, or GreenCo certification. Use results to improve processes. Measure scorecard or rating