Collaborative problem solving and development stood out as a major theme during the Global Print Konnect Conference – ‘Powering India’s Inkjet Journey’ held at New Delhi’s Aerocity on 14 February 2024. Addressing the opportunity to bump up inkjet output device manufacturing in India — Seiko Instruments, Kao Chimigraf, Meteor, People & technology, and Trijet made presentations and took part in the discussion that followed.
The presentation by Tri Tulidhar, director of Trijet, ‘Fluid Dynamics: Tailoring properties to meet industrial inkjet needs’ brought together many of the challenges and solutions faced by integrators and seemingly connected the dots for all the partner presentations.
Rheology is the science of the flow and deformation of matter and describes the interrelation between force, deformation, and time. Trijet focuses on the complex rheology of inkjet printing inks and has developed novel techniques to link fluid rheology to jetting behavior. The rheological properties of an ink may depend on different parameters such as deformation, processing time, processing rate, temperature, and more.
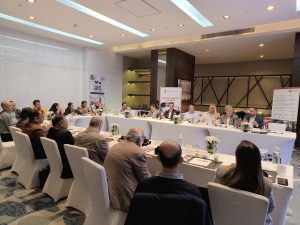
Tulidhar explained that ink and printhead are a merger of chemistry with physics (with a little bit of mechanics) – the yield of this combination arrives on the substrate. The application should determine the combination of physics, chemistry, and mechanics required and the fine-tuning to be administered for reliable changes and results. “A printhead’s work is to jet inks on a substrate – doesn’t matter if it’s solvent-based, water-based, or inkjet. But the fluid, the inks, and its dynamics need to be looked at from different perspectives,” he said.
He added, “What one may consider liquid could be considered solid on a different timescale, for example, glass is a high-density liquid and is believed to be a solid object. To formulate ink one needs to consider things on a mechanical timescale [and weight and size] — milliseconds, nanograms, and micrometers. This becomes an important aspect of printing, as regardless of the substrate, there’s always a time required to print, and a place to print, and it is necessary to ascertain the drop size of the ink needed. It is inconvenient to think of these aspects under general parameters because the time to print is in nanoseconds, place to print in micrometers, and drop size of the inks is in nanograms.”
Think of the ink as blood and the machine as the body which translates to a printhead being the heart whose purpose is to pump blood. If the pumping is more or less than necessary it creates a challenge and the final product will not be what was originally desired. “That is where the mechanical comes in with drive electronics that push the ink for the right drop, place, and time,” he said. It is also important to maintain and clean the printheads as ink clotting could be a big challenge and printers that can auto-clean their printheads is still a technology for the future to discover.”
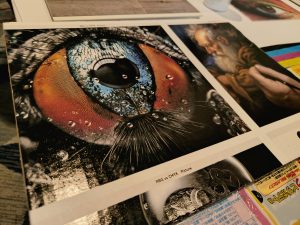
A collaborative effort is required between printhead manufacturers, drive technology providers, printhead maintenance, and ink specialists to push inkjet technology in India in the direction of high-quality home-grown solutions for multiple application opportunities. Presently if a printing defect occurs consistently, it leads to a spiralling blame game. The printhead maker will blame the ink, the ink provider will blame the maintenance of the machine, and so on, and amid all the confusion the production will come to a halt.
“We are all gathered here to tend to the problems as a team. A collaborative effort is a way to keep up with inconsistencies and other problems that may arise in the future. Inkjet has massive potential for printing on paper, flexible packaging, corrugated packaging, ceramics, and even textiles. It has a huge market in Europe and China and together as a collective, we want to project the opportunity for Indian markets and help in its realization with better technologies and efficient management,” he concluded.