During the Heidelberg Innovation Week that took place from 13 to 15 October this year, there was an interesting conversation between two European packaging printers which is of some relevance to Indian packaging printers and commercial printers migrating to monocarton production. The conversation was about their experience operating Heidelberg Speedmaster presses and how the technology helped them to increase production rates. Spain’s Temps Impresores shared the experience of its recently acquired Speedmaster XL 75, while Hungary’s Kartonpack spoke of the company’s Speedmaster CX 104.
Starting as a commercial printing business, Temps Impresores now derives almost all of its revenue from packaging. (About 98% of its revenues is from the packaging business while only 2% remains from the commercial segment.) The company was founded in 2004.
Temps’ Isidoro said that with the new Speedmaster XL 75 the company has succeeded in cutting the production time for monocartons. “Because of the new Speedmaster XL 75, we successfully reduced the production time because with its drying system there is no need to wait. We now process 30 jobs per day compared to 17 jobs per day previously,” Sanchez said.
In addition to the Speedmaster XL 75, most of the current equipment at the Spanish printer turned converter is from Heidelberg as well. It operates a Versafire digital printing press, a Suprasetter A74 CtP unit, a Speedmaster CD 74 4-color press, a Stahlfolder CH-66 folding machine, and a Polar N 115 Plus cutting machine. It also has an MK Promatrix 106 CSB die-cutter and an MK Diana Easy folder gluer from Heidelberg’s Chinese partner Masterwork.
Sanchez stated that his company is focusing on packaging sustainability and uses environmentally friendly inks and plates. In addition, all the production units have solar panels installed on the rooftops. “Every year we try to be better,” he said.
Kartonpack increase productivity by 25%
The Hungarian folding carton manufacturer Kartonpack has been using one of the first Speedmaster CX 104 presses for a whole year now. Kartonpack was a pilot user of the new Speedmaster CX 104 and based on this experience with its innovations such as the intelligent controls and the easy to change anilox system that the press introduced, it decided to buy the press.
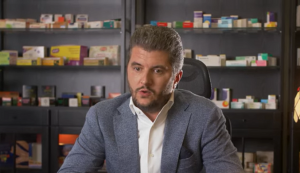
“The Speedmaster CX 104 was installed as part of strategic collaboration. Only one other European print shop had this opportunity, something we are extremely proud of. Taking into account our job structure, we’ve found that the new Speedmaster CX 104 fully meets our current and future expectations regarding flexibility, reliability, and quality. We’ve been particularly impressed by the system’s intelligent control concept and the coating unit’s high-performance levels,” said Kartonpack president and CEO Dr Sándor Uszkay-Boiskó.
Kartonpack commissioned the new Speedmaster CX 104 back in September 2020, amid the Coronavirus pandemic.
The new press has been in continuous three-shift operation at the company ever since. After just the first full month of production, the new press had already taken over the bulk of the production volume. The printing system is switched to a new packaging job several times during each shift. Given this job structure, the rapid changeovers on the Speedmaster CX 104 are particularly beneficial. The new coating unit developed by Heidelberg makes a key contribution to this speed.
“With the new CX 104, we were able to reach higher output speeds and shorter make-ready time. In the end, our productivity went up by 25%. Also, it is very important to us to improve varnish as we varnish 98% of our work. The time spent on replacing anilox cylinders has dropped by 75%,” said Nóra Teleki, Kartonpack’s production, and operations manager.
Our take – What Indian print business can learn
What can Indian printers learn or infer from this conversation? Naresh Khanna our editor and a longtime ethical technical consultant to the Indian print industry says, “Too often we overlook the experience of overseas printers, not realizing that we own and operate the same technology and often we have the same global customers. In fact, in many cases, we can sometimes make a bigger leap with technology than overseas print businesses because we have bigger skill gaps on the shop floor and fewer modern assets to replace.
“We can also learn that a commercial printer migrating to cartons may be better off with a B2 press that has newer technology as quality, value addition and productivity may bring better revenues than simple carton volumes on B1 press. From this conversation which Heidelberg presented as a part of its digital marketing in pandemic conditions, we can also learn that investments in the pandemic do not need to be stop gaps, they should preferably, embrace new productivity technology especially in areas such as setup and makeready and coating.
“Please also note that in this conversation, the presses are described as ‘systems’ which in this case means that their functionality, efficiency, and condition can be digitally monitored. This is a change in the way of thinking about print that we need to bring to our businesses and the thinking of our operational teams. It requires a more transparent and democratic atmosphere on the shop floor that we can bring about with the use of systems technology if we are willing to give access to the team. It is the shop floor teams that will have to increasingly create both the goals and the performance reviews since this is a continuous process and not just once a week or once a day. This is already happening in some of the best Indian print businesses.”