Koenig & Bauer Durst has launched new water-based orange and violet inks to ensure food safety compliance for primary packaging and extend the colour gamut. This will positively impact upon brand management for brand owners, particularly in producing colour saturations on packaging samples and spot colours. With around 50% of corrugated packaging in food and beverage, the ink set ensures that converters can invest knowing they will be ahead of the increasingly complex regulatory change curve.
Koenig & Bauer Durst is a young company in the digital printing systems market. The two parent companies Koenig & Bauer and Durst Phototechnik each hold 50 percent of the shares in the joint venture founded in 2019. The company develops, manufactures and markets single-pass digital printing presses for folding box and corrugated board production. It brings together the technological focus and market expertise of the two parent companies – both in the development of digital printing systems and in mechanical and plant engineering. The company is integrated into the service and sales structures of Koenig & Bauer and Durst Phototechnik and currently employs its own staff.
Koenig & Bauer Durst has also announced new automation features for the Delta Spc 130 FlexLine Automatic that will ensure high productivity and can be integrated into existing customer workflows. Enhanced image quality and special effects, as well as cost reduction, are among the benefits from a new digital primer. New effects that are possible include print embellishment on corrugated board with uncoated media.
The Delta Spc 130 FlexLine Automatic combines mechanical design with accessible sub-assemblies and selected components. It is claimed to guarantee durable quality, high performance and reliability. It can manage small formats from 500 x 600mm through to very large formats with maximum dimensions of 1,300 x 2,800 mm and print a maximum thickness of 12 mm with water-based, food safe inks. The Delta Spc 130 FlexLine Automatic machine includes non-stop feeder, four-colour single-pass printing, drying and cooling section and non-stop stacker.
The Delta Spc 130 is part of the Koenig & Bauer Durst portfolio of solutions for corrugated converters. Another is the CorruJet 170 that post-prints sheets of corrugated up to 1.7m wide at up to 135m/min. The B1 6,000sph VariJET 106 completes the line-up and targets the folding carton market.
The presses meet the stringent requirements for food safe primary packaging utilizing proprietary water-based ink technology and are designed with core technologies to provide automated, productive, food safe printing systems. They deliver shorter response times, more variants, shorter run lengths, individualization, and enable more and more small value orders. They also answer the increasing customer demand for brand security, sustainability and the ability to meet brand owners’ requirements for multichannel communication including eCommerce.
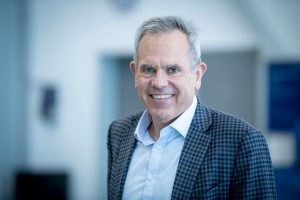
Robert Stabler, managing director, Koenig & Bauer Durst, said, “All these innovations for our Delta Spc 130 FlexLine Automatic are designed to exceed market needs. Food safety and packaging is a constant topic of conversation. These new water-based inks will ensure food safety compliance for primary packaging and extend the colour gamut, which, in turn, will impact positively on brand management for brand owners. Brand owners are demanding that new production methods are reliable, compliant and cost-effective while converters need to have the capabilities and competencies to mass customize without any compromise on quality.”