K&B has just released a new generation of the Rapida 76 sheetfed offset press. The B2 press (standard sheet format 530 x 750 mm; special format 605 x 750 mm) has a high level of automation, a minimal footprint, and peak printing speeds of up to 18,000 sheets an hour.
Automation functions characterize the Rapida 76 as an extremely efficient press, with high-performance features including DriveTronic dedicated drive components, which eliminate gear systems and provide for both simple handling and parallel processes during job changeovers and make-ready. There are full preset capabilities of all press functions and the ErgoTronic console with a wall screen. The Rapida 76 has additional decentralized touchscreens for maximum ease of operation.
Highly configurable Rapida 76
For as many different applications as possible, up to 11 printing and finishing units can be combined to configure a Rapida 76 for specific production needs. That could mean a ten-color press with an automatically convertible perfecting unit for 5 + 5 production – possibly together with an additional coating tower to allow printing of covers, for example – or packaging presses with double-coating facilities for the production of pharmaceutical packaging.
Further variants incorporate raised foundations to accommodate higher piles with board substrates or various delivery extensions for coating applications. Ink duct dividers can also be chosen to enable rainbow printing. Thanks to a comprehensive range of measuring systems and optional facilities for inline sheet inspection, the Rapida 76 can be configured for many special applications, including the production of security documents.
The new press is no less flexible when it comes to compatibility with different ink and coating systems. It handles both conventional and UV inks and coatings with equal ease. Beside IR/hot-air drying systems, various UV, HR-UV and LED-UV systems are also available.
Special K&B features
The Rapida 76 offers unique features that benefit users in their daily work but are not yet common in most half-format size presses. Inking units that are not required for a particular job can be disengaged from the press drive. This reduces roller wear and cuts make-ready times. When production is to be resumed, the units concerned are re-engaged at the press of a button.
On the Rapida 76, unbent plates can also be mounted, irrespective of whether an automated or simultaneous plate changing system is in use. This feature was introduced on the new K&B Rapida B1 press in June at the K&B Live virtual demonstrations. It will likely permit even higher automation of the press room if needed.
With simultaneous plate changing, all the plates on the Rapida 76 can be changed in just 45 seconds. In combination with CleanTronic Synchro, the blankets and impression cylinders and the ink rollers – can be washed parallel to plate changing. This shortens make-ready times dramatically and leaves much more time for actual production. The same applies to automated coating forme changes.
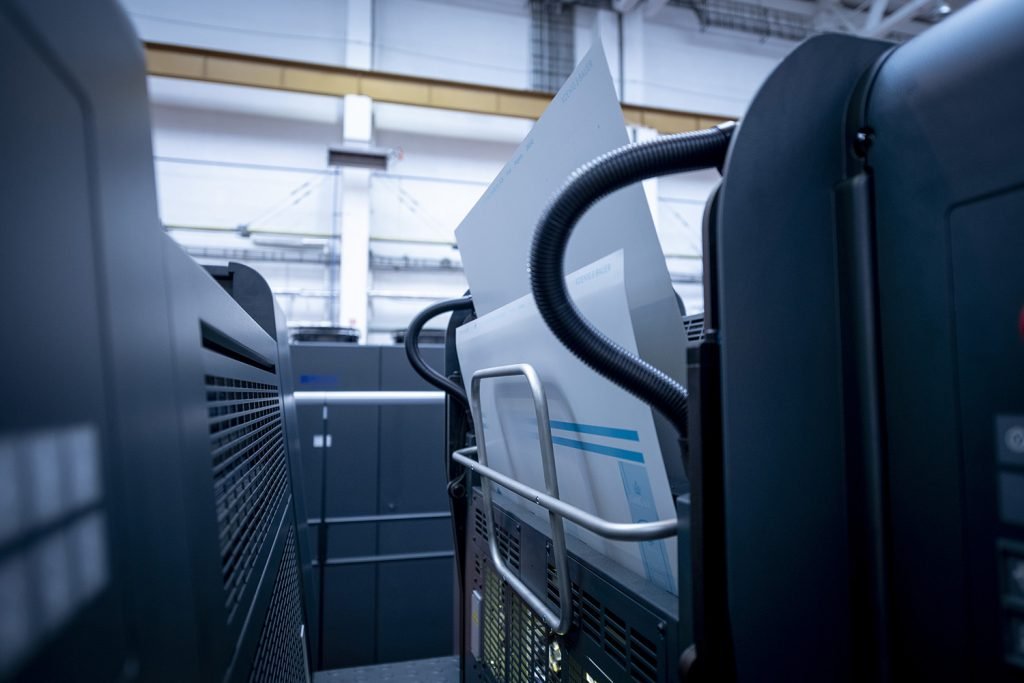
Wide range of measuring and control systems
Application-orientated measuring and control systems contribute to faster make-ready, reduced waste, and consistently high and stable print quality. The Rapida 76 can be configured with systems for register measurement and control, color control and sheet inspection. All inline systems operate with a common camera, which reduces maintenance requirements and simplifies handling.
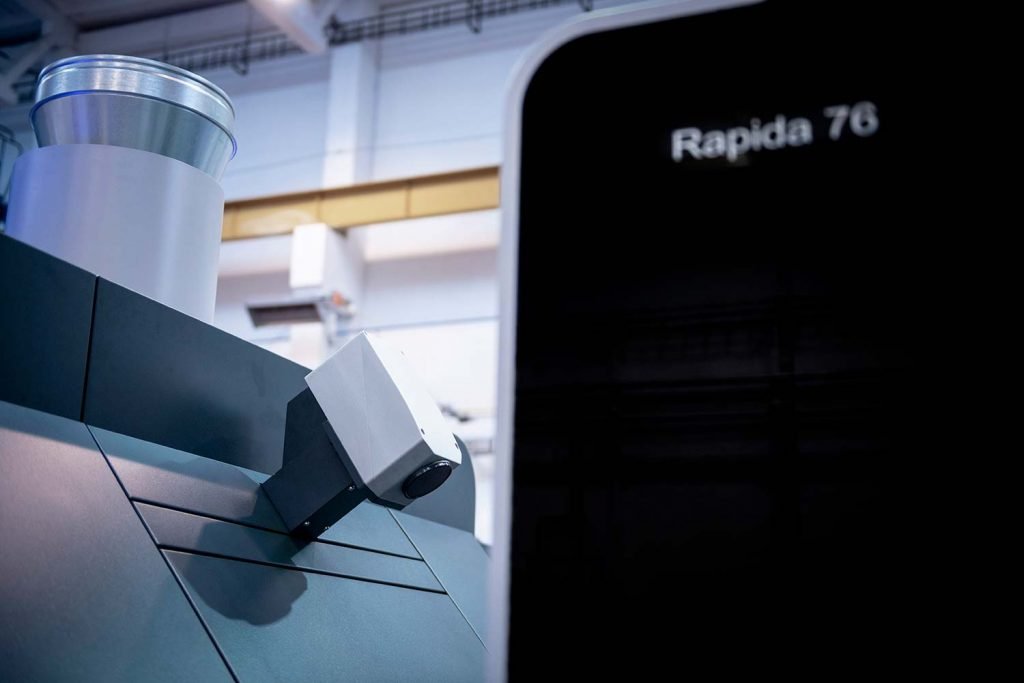
In a full-featured setup, ErgoTronic ICR controls the register by way of a single sheet placed on the console, while QualiTronic ColorControl provides for convenient color adjustment. The camera system installed after the last printing or coating unit or after the last unit before perfecting automatically determines the optical densities. It controls the ink keys without further intervention. As an option, the system can be expanded to implement color control according to grey balance (QualiTronic InstrumentFlight). QualiTronic PDFCheck carries out the inspection of the printed sheets and comparison with the customer’s PDF as the basis for uncompromising quality.
Digital services at the press of a button
Many digital services surrounding the Rapida 76 help reduce unplanned downtimes, facilitate convenient and barrier-free maintenance of the press, and permit anonymous comparisons of important performance parameters with other presses in identical configurations. The options range from PressCall for optimization of communication with remote maintenance engineers and VisualPressSupport to enable a better description of the reason for a remote maintenance call. The remote support functions use photos (with extensive commenting functions), texts, videos, and audio, via Performance Reports and Press Inspection Reports, through to the first instances of predictive services based on artificial intelligence methods.
In this context, the Customer Community is a central point of contact bringing all service offers together under one roof. Users and the manufacturer have access to an identical information database, meaning that they are all on the same page.